Expert story
Waste treatment - a radical 100 year transformation
An excursion with David da Silva
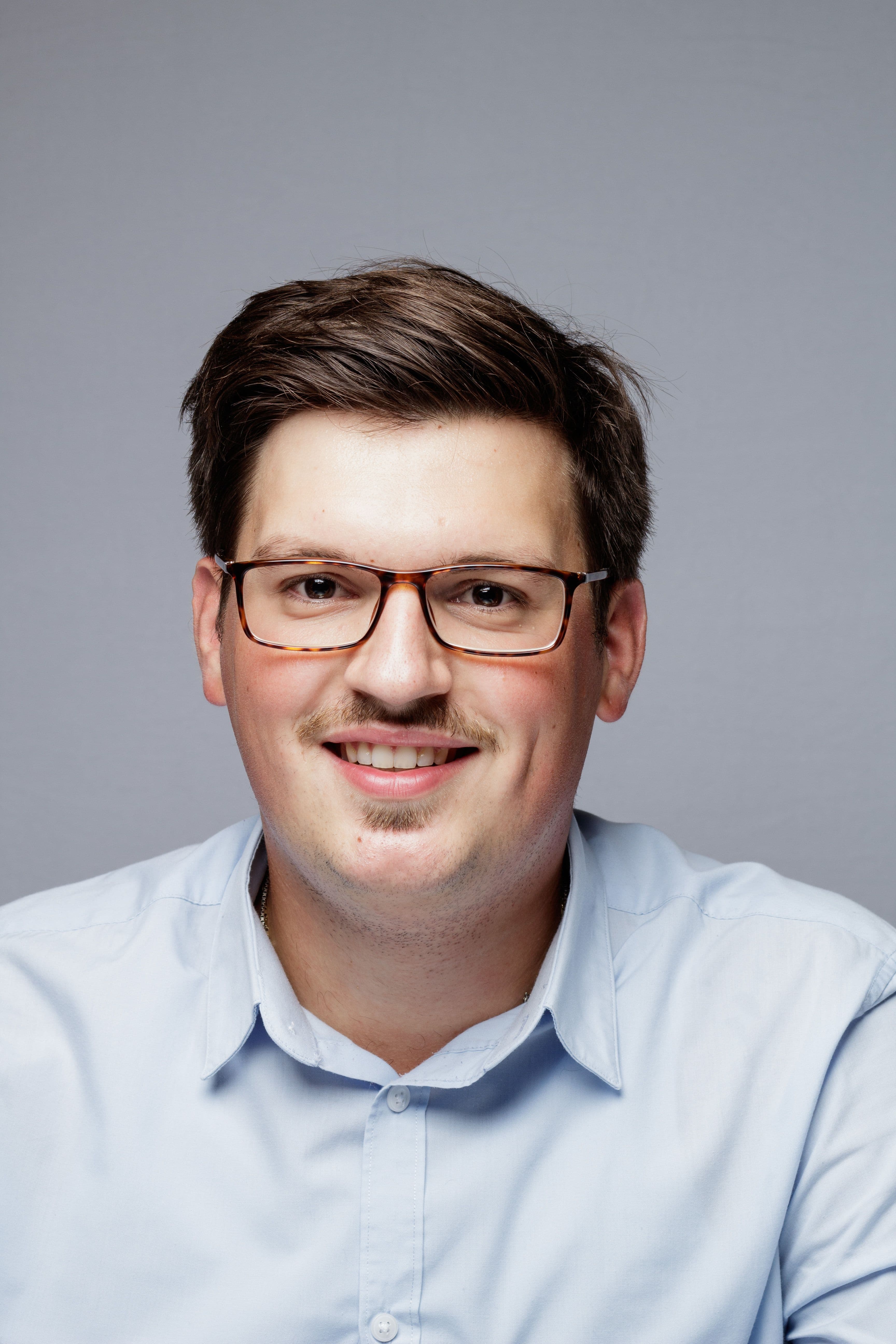
100 years of waste treatment in Switzerland
A brief chronology
David, you’re a mechanical engineer by training – how did you end up working in the area of waste and energy at TBF?
The big debate among my fellow students was always whether to go to a major company such as ABB or Siemens, or whether we were better off joining a planning firm. At the big companies, you’re usually responsible for a sub-division and something very specific. At TBF, however, I see the entire process, starting with the initial outline of the idea before moving on to planning and liaising with the authorities and ultimately to construction and commissioning. I can step into the process at any time. It usually takes about 10 years from the initial idea until the incinerator starts operating. That’s what makes TBF such an exciting and varied place to work. You might be in contact with the bird protection officer in the morning – to ensure that breeding boxes are included in the plans for a new plant – and then spend the afternoon working on the detailed verification of the turbine blades. In other words, the work is extremely wide-ranging and it’s this mix that makes it so special. The main difference between TBF and other planning firms is that we don’t just assume responsibility for one stage of the project and then pass it on to the next specialist. We have the opportunity to watch our developments and plans unfold first-hand as part of the 'reality check’ during construction and commissioning, and to collate the resulting knowledge and experience and pool it with our colleagues. By doing so, we ensure that our expertise remains within the company. We’re assigned a task and can then decide for ourselves how we want to meet the objective – and that’s really inspiring.
When did you join TBF?
I originally joined TBF as an intern in 2012 after graduating from ETH Zurich as a mechanical engineer. An internship was advertised at the Forsthaus energy centre Bern on the plant that TBF as overall planner implemented on behalf of Energie Wasser Bern EWB.
Did you build a classical waste-to-energy plant?
No – to be precise, it was a waste-to-energy plant in combination with a wood and a gas-fired combined heat and power plant. I joined the project as an intern during the construction stage and helped my colleagues with the commissioning. Afterwards, I decided to go straight on to do a master’s while continuing to work at TBF alongside my studies.
During that time, the first big win-win situation was my master’s thesis, for which I modelled and programmed a tool that can be used to simulate incineration processes. In other words, it allows you to predict not only the amount of waste gases but also how much fresh air should be introduced into the incineration process and at what temperature. In simple terms, the question is always: if I burn 1 kg of waste, how much residue is produced, how much heat is generated and how much steam can be obtained? The incineration of waste leads to the evaporation of water, which can be used to drive a turbine in order to produce electricity. The heat generated in the process can be supplied to households via district heating networks. And how much energy can be recovered from this process in order to power a turbine for electricity production? In short, we can use the tool to calculate all the flow of air and energy in the system.
And the tool is already in use?
Yes, the tool is now used for every project. That’s another thing that makes TBF unique – tools are almost never bought in, but are instead developed within the company wherever possible. That allows us to provide customers with quick and efficient access to calculations, and it means we always retain the necessary expertise in-house. This stems partly from the fact that we have a steady stream of interns working for us, and accordingly maintain close relationships with universities such as ETH.
So does that mean that customers first determine how much energy they want to use to build a plant?
No, the customers are usually waste-driven. That means they know how much waste they have to recycle and how much district heating they have to provide. The decision is usually based on the two parameters of waste input and heat generation. The difference between these parameters is the electricity production, which in turn can be sold. For waste treatment companies, electricity production is generally the only variable in play – the other two parameters are fixed.
After all, the trend in waste treatment is strongly linked to population growth. What is the situation like today? Are plants becoming more and more efficient, or are we simply building more of them as the population grows?
Actually, waste treatment technology did not go through any major development steps between the Second World War and the 1970s. Until then, the focus was more on preventing disease and epidemics, so it was felt that landfill waste had to be incinerated. It was not until the 1980s that the need to optimise the treatment process from both an economic and an environmental perspective became obvious – that is, by recovering energy and installing flue gas purification systems to tackle harmful emissions. Today, we can say with a clear conscience that what comes out of the chimneys of modern waste-to-energy plants has been rendered virtually harmless to the environment. I wouldn’t go so far as to describe them as purification plants for ambient air, but we’re getting to that stage. ;–)
In Switzerland, the graph of population growth shows a strong upward trend, and there is more and more talk of the country’s population reaching 10 million. How can we ensure that waste treatment is able to cope with the rapid pace of growth?
From an economic perspective, the best thing would be to build one ‘superplant’ for the whole of Switzerland. But from an environmental perspective, it wouldn’t make sense to have vehicles transporting waste over the length and breadth of the country. Energy recovery is also regulated and organised differently from canton to canton, as they depend strongly on their district heating networks. Accordingly, waste treatment will continue to be organised at the local or regional level. Today’s technology is very sophisticated. The key thing now is to optimise it for regional circumstances in order to make the best possible use of capacity. Here, the focus is on the mix of plants – and that’s just classical engineering work.
Of course, not all waste-to-energy plants in Switzerland are built by TBF. What’s the difference between you and your competitors?
To go back to our company values – holistic, authentic, smart – I take the view that our organisation is better at thinking outside the box. We don’t simply build a new plant somewhere; rather, we take the time to think about what will be needed in two or three generations, so that the plant can be optimally equipped and expanded. Our advantage is that we not only employ mechanical engineers, but also have all the other specialist areas under a single roof. Accordingly, if we’re working on a project and realise that the plant needs to be bigger than originally planned, I can discuss it directly with my civil engineering colleagues and get a first-hand idea of whether the planned construction will be able to cope with the new parameters. Fewer interfaces increases our efficiency and allows us to provide the customer with quick and agile service.
How do you picture the future of waste treatment?
That’s hard to predict. The driver of technical progress has always been people, and society is in a constant state of flux. We observe and record these developments in the form of ‘megatrends’ – such as population growth, further increases in the separation of plastic waste, and decarbonisation by 2050. Indeed, CO2 emissions from our plants is an exciting area that we’re currently researching and working on. While CO2 is neither a pollutant nor toxic, it does contribute to the global greenhouse effect. The problem is that there’s no way to make CO2 harmless. Substances such as nitric oxide, can be converted or filtered out using catalysts, but CO2 is currently released into the environment. One idea is to separate CO2 out from the flue gas in an additional purification stage, liquefy it and store it deep underground. The goal is that under the enormous pressure at these depths, CO2 would be converted back into fossil carbon, thus completing the cycle. Here, our relationship with the universities – and specifically with ETH – comes back into play. Through close coordination with ETH, we’re able to divide tasks up smartly and efficiently. For the time being, we’re dealing with the plant technology while ETH handles the transport and logistics as well as calculating whether the planned investment makes sense – after all, transport to the storage locations also generates CO2 emissions. Overall, the whole exercise must be worthwhile for both people and the environment. In terms of CO2 removal during flue gas purification processes, we’re working with KVA Linth (Canton of Glarus) on something that has not been attempted in Europe before – thus demonstrating our pioneering spirit. We’re confident that this technology will represent another key step towards the decarbonisation of waste treatment, and make a substantial contribution to a clean and sustainable future. As with all technology and innovations, however, it’s important to recall the wise old saying: 'Avoidance before recycling before disposal.'